AFM Nanoindentation Association
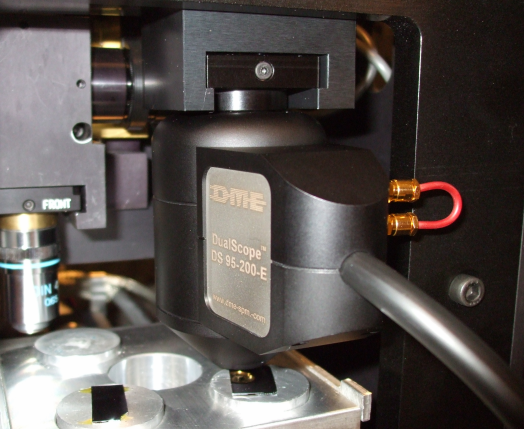
The capability of imaging indentation prints at specific intervals after an indentation experiment has always been of great interest for user’s.
The unique configuration of a complete AFM head right next to the nanoindentation column can provide very valuable information, especially for materials with time dependent properties.
So far, the compromise of using the indentation tip for imaging, or using an external imaging instrument has strongly limited the quantitative characterization of these properties.
Imaging with the indentation tip results in low quality images (shadow effect), lower resolution and sensitivity to the relief The use of an external instrument ( AFM, SEM,…) enables high quality images but requires more time to locate the indents of interest and renders time-dependent analysis very difficult to perform.
The unique combination of the 95-200E integrated within the Agilent Nano Indenter enables a series of analysis unavailable before, such as, quantitative time dependent analysis of relaxation of the indentation print, repeated indentation experiments with imaging between each indents, etc…. The original integration of the AFM head in the Nanoindenter gantry create a third complete and independent test axe to study the sample surface. It does not disable the optical microscope provided in the Nano Indenter, but rather, complements its purpose by making optical observation, mechanical testing and imaging analysis as simple as clicking on your screen the position of
interest. This third visualization/imaging axis gives unprecedented flexibility and power to the Nano Indenter.
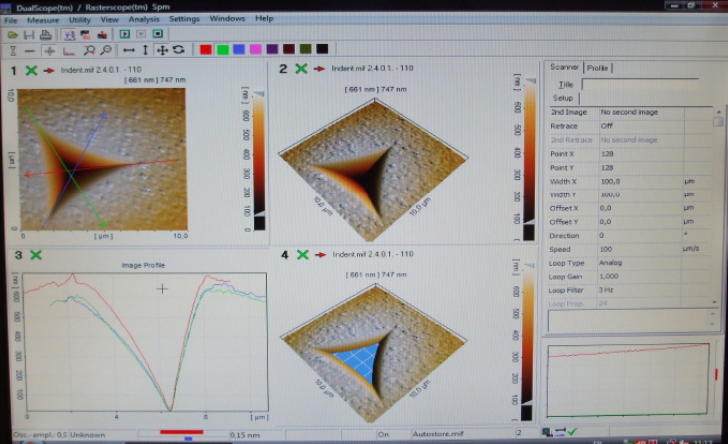
Through the 95-200E AFM analysis page, the indentation volume (swimming pool concept) or the contact area can be accurately measured. The pixel size allows the three dimensional measurement of the residual
indentation depth and pile up. In addition, the actual shape and dimension of the indentation print can be easily analyzed and interpreted using classic analysis methods developed by colleague researchers. Verification of
the Oliver and Pharr or Loubet method to determine the actual contact area, hint, the properties of the material is easily performed.
A new capability given by the AFM software is the ability to create a video of the elastic recovery by adding a number of images of the same point with the time.
The analysis page offers enhanced flexibility to study the surface from a roughness parameters, mechanical
properties, or three dimensional morphology stand point, depending on the specific interest of the user
AFM specifications:
Optical view with separate CCD camera for the AFM part.
Scan area for AFM 200 x 200 micron X,Y, 15 micron Z. Topography image as well as phase image in the normal SPM modes, plus various modes for characterization of electrical features in the surfaces by means of E-model
(optional). AFM scanner probe change is extremely easy